Heat Tamers
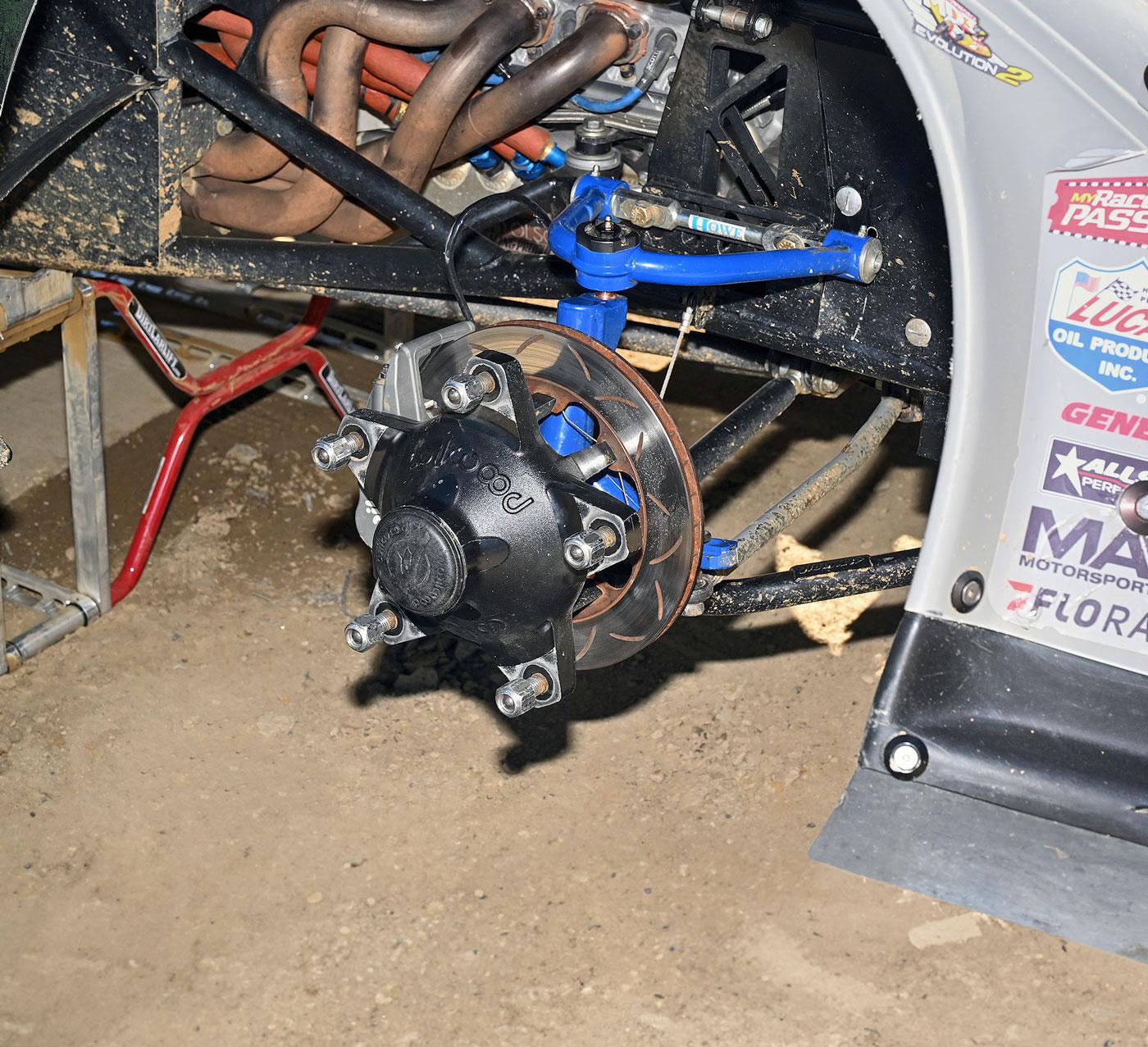
Teams and manufacturers wage a constant battle against brake heat. Here’s expert advice about how to control that heat and complete the race to the checkered flag.
Excess brake heat in a racing environment is something that’s hard to ignore. Fans can’t help but notice the glowing brake rotors of the cars on track, shining like molten donuts and throwing off heat you can practically feel in the grandstands. Drivers know that sinking feeling in the pit of their stomach when, late in a race when brakes have been pushed to the limits, a brake pedal no longer responds to commands.
Parts manufacturers are well aware of the detrimental effects of out-of-control brake heat and offer an impressive selection of rotors, calipers, pads, and fluid to keep racers on track. The demands of different forms of racing offer constant challenges, but manufacturers often work directly with teams to solve problems and develop new products.
“No matter what brake system you’re running, heat is the killer,” said Dave Brzozowski of Wilwood, Camarillo, California. “Fluid is very important because heat will immediately attack fluid and its ability to take it. Then you have things that are all caliper related, so you have the heat dissipation, seals, pads. Pads, when they get extended heat periods or high heat, certain ones can become more compliant. They might look good, but they get a mushy feeling or soft, and lose some of their density.”
High levels of heat will become noticeable to a racer in a variety of ways. “There’s pretty much two kinds of fade. There’s either pad fade or fluid fade,” said Mitch Bloom of Hawk Performance, Medina, Ohio. “If the fluid starts to oxidize and get bubbles in it, that will result in a spongy pedal. That’s what most associate fade with. Pad fade is more of, the brake pedal feels fine, but the car is not slowing down. Or the characteristics of the pad are deteriorating and maybe its bite isn’t strong, or maybe the friction isn’t as linear with the pressure you’re applying.”
High heat can then create a cascading effect throughout the braking system. “When the friction material starts to overheat and go over its maximum temperature range, pad wear will accelerate really quick,” said Edwin Mangune, also with Hawk Performance. “You’ll also get glazing on the pad surface and on the rotors, which will affect stopping power. You’ll get excessive pad transfer onto the rotor. You’ll see a heavy build-up of the pad material on the rotor, which will cause an uneven surface, so you’ll get feedback from the pads to the brake pedal. Which can definitely annoy the driver and break his concentration.”
Teamwork
When it comes to addressing brake heat, there’s no better strategy than getting in the trenches with race teams and working through the problems. Our sources were hands-on when it came to interacting directly with racers.
“New Smyrna Speedway is a pretty hard-braking place. This year in particular, brakes are glowing around there for 100 laps. It’s not uncommon to see front brake rotors glowing,” Brzozowski said. “I ran three different pad compounds at New Smyrna with teams back in February clear up until May and June. We used all that to come to a conclusion that ‘This pad is something we want to move forward with,’ and we instigate it. That’s how we go about it.”
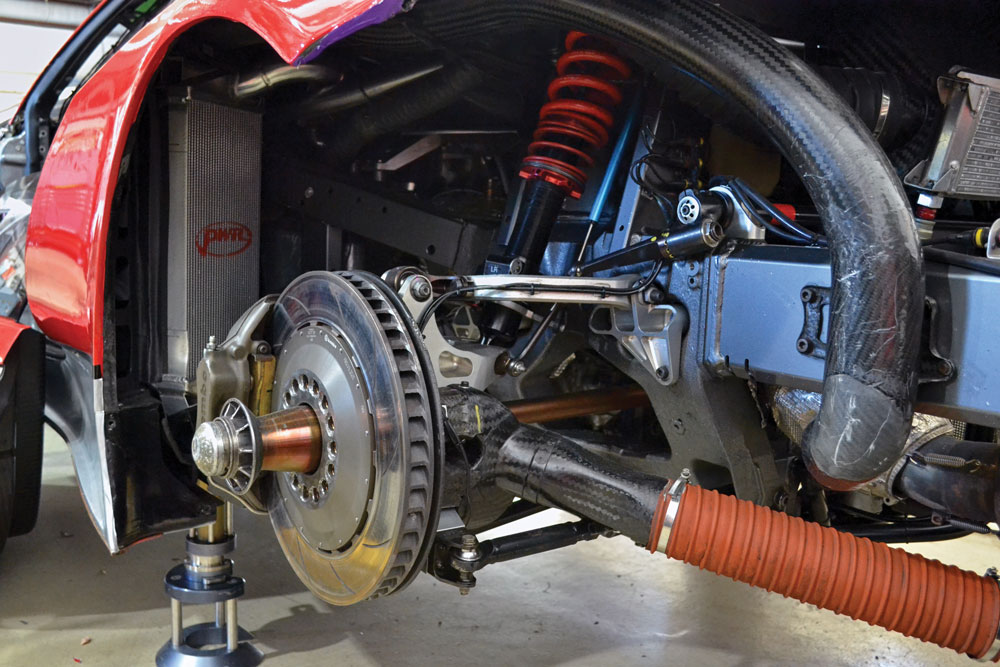
Halo by Orthene in Harrow, Middlesex, United Kingdom, specializes in brake fluid. The company’s flagship racing product is Halo P1. “Halo P1 was formulated after over 18 months of research and discussion with a number of top-tier race teams and performance OEMs,” said Daniel Stafford. “It has taken Orthene’s near 50 years’ experience specializing in brake fluid to create the best racing brake fluid we’ve ever produced. It’s formulated for track-only usage, which means that we’ve been able to focus on achieving the best performance, rather than needing to adhere to some of the requirements for road usage that limit what’s possible from a performance perspective.”
When developing P1, specific challenges from different racing series had to be considered. “Closed-wheel teams were using unsuitable fluids for ABS-equipped systems, which was causing poor performance and costly damage to ABS systems. P1 is fully compatible with ABS, as are most glycol or glycol ether-based brake fluids, as opposed to mineral, silicone or silicate ester-based fluids,” Stafford said.
“In rallying, an issue was teams using fluids with high viscosity. Certain brake fluids are highly viscous at low temperatures, which make them unsuitable for cold weather environments,” he continued. Another focus of P1’s development was heat soak during pit stops, which causes the pedal to be almost completely lost for the lap coming out of the stop, he said.
Sometimes working directly with race teams takes manufacturers in unexpected directions. “I was approached by a Trophy Truck team for the Baja 1000,” Mangune recalled. “The Trophy Truck guys several years ago would have to do one brake pad and rotor change to finish the race. Cooling was not an issue, and they couldn’t run any brake ducts because all they were going to get was foreign object debris being forced into the brake system. I went out to Barstow [California] with the teams and did some testing, and I brought a few pad materials I thought would work. One in particular was DTC-70. Back then, it was our highest torque pad with the highest temperature range,” he said.
“It solved the problem at Barstow in testing, so when it came to the real scenario at the Baja 1000, there were four or five cars that were on that pad. We weren’t really known in off-road back then, but after those trucks finished the race on one set of pads and rotors and said they had the best brakes ever, we became instantly popular.”
In a different corner of the racing universe, Mangune worked with a team in vintage racing to tackle overheating brakes. “It was a 1969 Camaro in SVRA Group 6. No matter how big the cooling vents were that the team put on the car front and rear, it couldn’t keep the brakes cool enough,” he said. “Because it was a vintage racer, they had to use the brakes spec’d for that class, which were the stock brakes basically. What the team did, and I was working with them very closely on this, was utilize a bigger rotor, a bigger heat sink.
“It was the same diameter because that was the call-out. But they didn’t say anything about the width, so he added more mass by going with a wider rotor, which gave us wider cooling vanes between the rotor plates. To do that, he made a spacer on the caliper to accept the wider rotor. While we did that, we made thicker brake pads for him. The thicker brake pads allowed the heat to dissipate before it transferred to the rotor and the calipers and the rest of the brake system.
“Everything we did was working better, but still not good enough, especially at tracks like Road America. So what he did was, on the intake ducts—which were huge, 3 or 4 inches, trying to maximize the airflow through there—he added bilge pumps from boats, used to evacuate water from the bow, which moved a lot more air than the vents did aerodynamically. That really helped manage the heat to keep the brake temperatures down. The stopping power was maximized as opposed to running hot and degrading,” Mangune said.
Changing Demands
Nothing stays static in racing for very long, and brake development is no exception. Manufacturers are constantly developing new products and solutions that will keep heat at bay. “There’s a lot of work that goes into the pad side of things. It’s a never-ending battle. You never can just sit there on your laurels and think you have the cat by the tail, and not think of the future,” Brzozowski said.
“Advancements in brake fluid technology have largely followed the new requirements of innovation within motorsport, be that the cars, parts, design, or regulations e.g., increasing grip-to-power ratio. These advancements on track require new formulations with new properties and are generally achieved through innovation in the production process, base materials, and additive packs,” Stafford said.
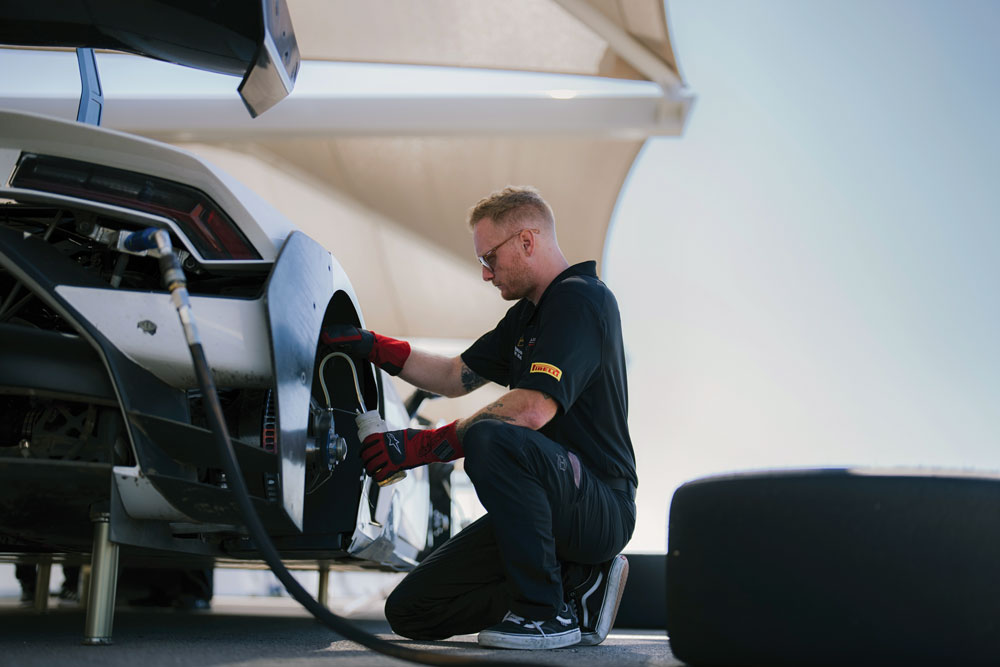
“There’s still a lot that we can do with brake fluid, and new avenues to explore,” he added. “In theory, we could produce tailored fluids for short track and long track, wet race versus dry race, and different atmospheric conditions. One property that has caught the eyes of the Formula 1 engineers is specific density, and we could potentially take 20–30% of the weight out.”
Larger trends in the automotive industry also guide brake development. “OEM cars, compared to 10 or 20 years ago, are much heavier and make way more horsepower than they did,” Mangune said. “It’s the same in race car classes. Trophy Trucks now are way more than the 7,000 pounds they weighed a few years ago, and making over 1,000 horsepower, whereas back then they were making only 700 horsepower. So we’ve stepped it up with our DTC-80, which we’d already had, but the same teams approached me because their trucks were heavier now and making 1,000 horsepower.”
Halo by Orthene has also followed the increased weight of modern race cars and adjusted its brake fluids accordingly. “A high boiling point is often used as a selling point. But the high boiling of Halo P1 enables the low compressibility of the fluid to be maintained even at extremes of temperature,” Stafford said. “That’s an essential attribute not only for closed wheel hypercar race series, but also saloon car racing series such as BTCC where vehicle weights have increased dramatically due to increased safety requirements and also the hybridization of powertrains. To the driver, the combined effect of high heat resistance and low compressibility across a wide temperature range results in a pedal that feels and operates consistently for the duration of the race, allowing precise modulation of the brakes.
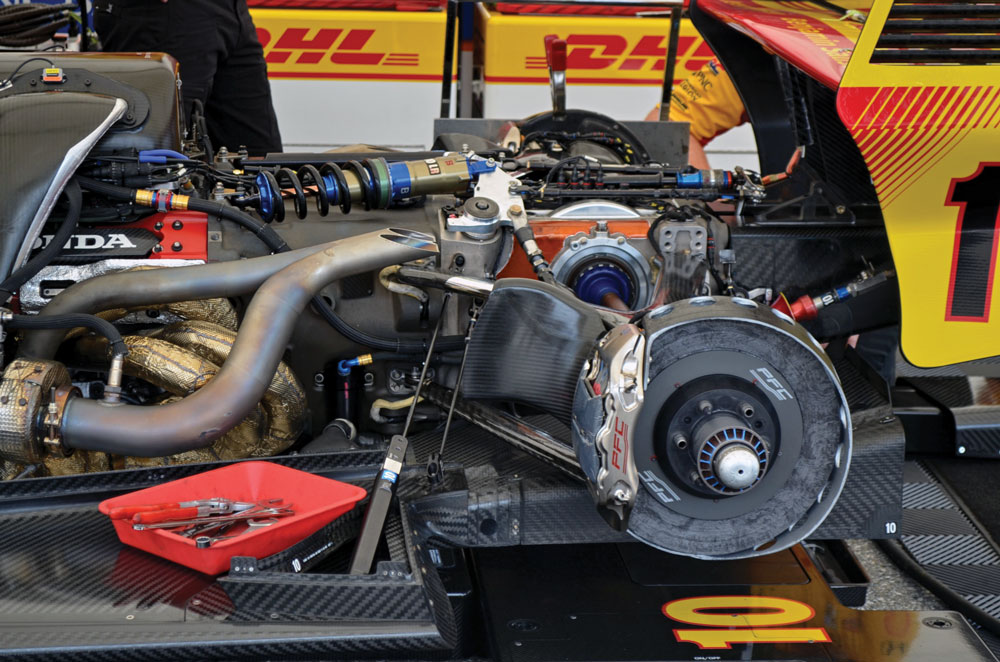
“While a high boiling point is necessarily important, it is the way that the brake fluid responds to temperature that is critical. Ideally you want as stable a compressibility profile as possible to give a consistent performance over the widest temperature range. This will give the driver a firm pedal feel, allow them to maintain the same braking points lap after lap, and give them confidence in the car.”
Hands-On
While parts manufacturers tackle brake heat from a product perspective, there are many things racers can do to help themselves when planning car builds or working through the racing season.
“The other thing about cooling—and this is where people miss the boat a little bit—is the fact that when you have a rotor that is a vented rotor, a curved vane rotor, the whole purpose of a curved vane is to act like a fan internally,” Brzozowski explained. “So you want to force the air to the center of the rotor to have those vanes moving to draw the air between the inner and outer face to help cool the rotor. Some people will just take a hose and a duct, and they’ll flow it to the face of the rotor. That may accomplish cooling one side of the face or pad, it may serve some purpose. But to truly cool a brake rotor and make it work, the ducting is everything. That’s why the center is really where you concentrate your work to cool the rotor. People will make ducts then to actually cool the caliper. They’ll do two things: caliper and then the rotor.”
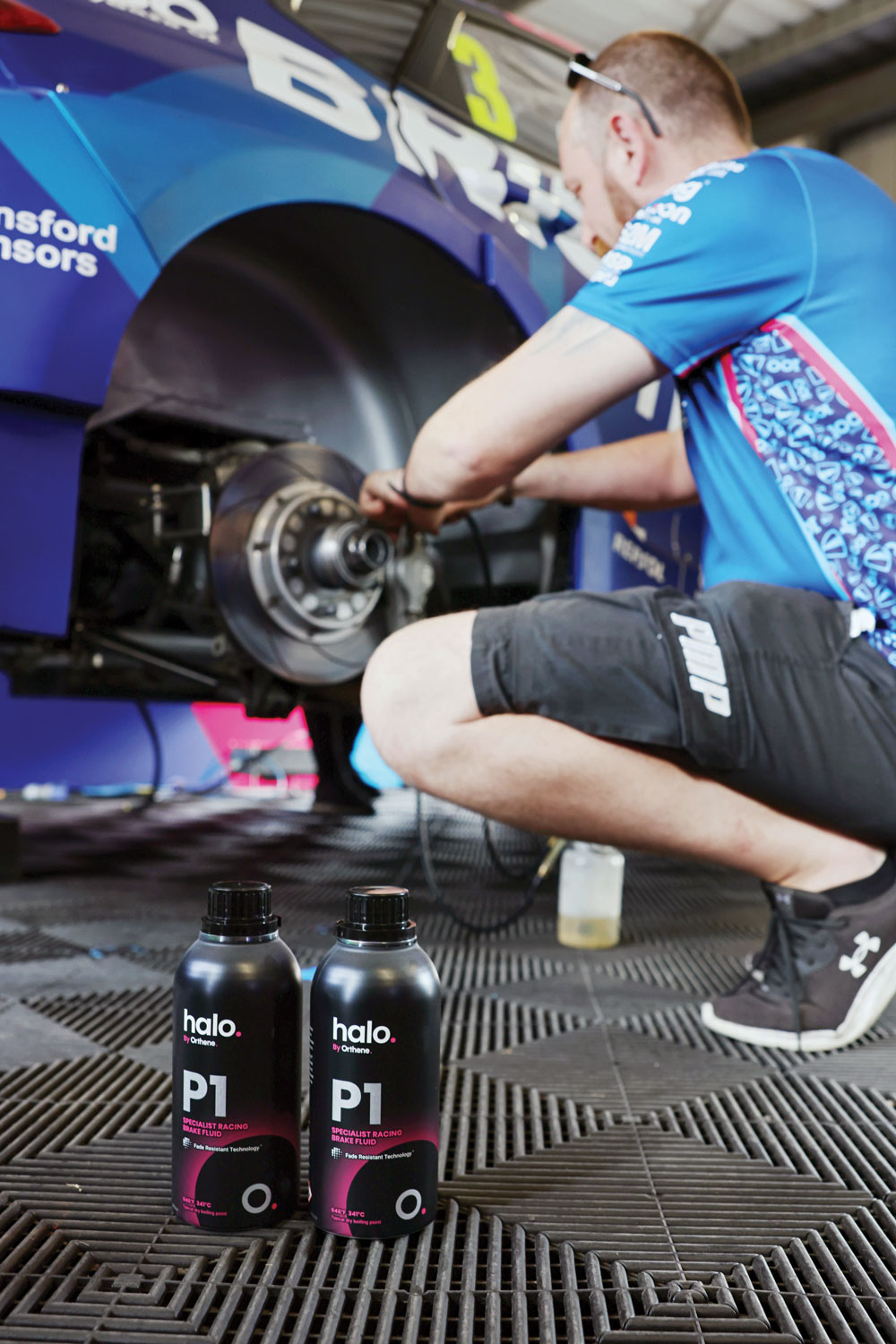
As with other aspects of motorsports, a bigger number is not always the optimum solution. “When we developed our brake fluids, of course we developed them to match our different friction profiles. For example, a race team could be out there with our highest torque, highest temp pad compound, which is DTC-80,” Hawk’s Mangune said. “But a mistake that often occurs with race teams is they’ll use the very best high-temp fluid that doesn’t break down, but the problem is that fluid will never boil, never get hot enough to break down to where the pedal will start getting soft. So the driver will not have any indication that he’s overheating the brakes. And he’ll just burn them down to nothing. With our fluid, even our 660, which matches our pad compound profiles, it will give the driver an indication that the brakes are overheating because the pedal will get soft. So the driver will know, ‘I’ll need to save my brakes.’”
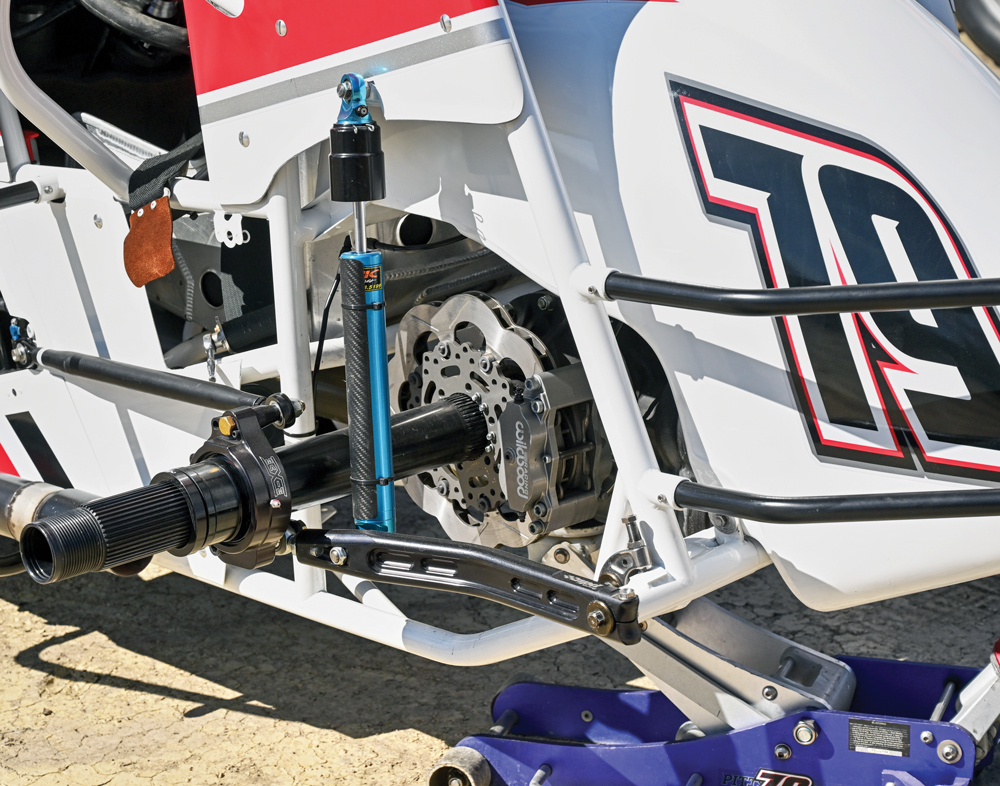
Shiny new parts play their role in minimizing brake heat, but regular maintenance plays just as big a role. “On a normal weekend racer, whether it’s a big block modified, a sprint car, even a tour-type modified, there are no real brake ducts on an open wheel car,” Brzozowski said. “But on those applications, a lot of it is maintenance—ensuring that you’ve got really good fluid that can take whatever you’re dishing out to it and ensuring that you’re doing your lead process and staying on top of your preventive maintenance. You do all that stuff, and nine times out of 10 you’re not going to have any issues.”
SOURCES
Halo by Orthene
halobyorthene.com
Hawk Performance
hawkperformance.com
Wilwood
wilwood.com